Why is it important to check purchasing processes?
It is one of the most important business processes of a purchasing department. Control the risks associated with the process when purchasing for your company; preventing fraud is vital to maximize savings and meet legal requirements.
You should periodically check your purchasing processes and create a list of these checks for later review.
Approval Process
Once an order is placed, it is important to develop a system or set of guidelines that are created to confirm orders placed and shipping amounts. Each action on your checklist will facilitate your audit. You will have a transcript of the tasks and can identify what is missing.
While conducting the audit, signatures should also be checked to ensure that the integrity of your approval process is maintained. The date of each transaction should be confirmed. For purchases made without confirmation that the transaction is eligible, an investigation must be carried out. Such investigations help uncover fraud and negligence.
Eligibility of Seller
Determining how suitable the suppliers are for you and for your purchases is another important aspect in the control of the process. Finding the right suppliers plays an integral role in your company's profitability. Your controls should be adjusted in such a way that only the appropriate suppliers are used.
In the purchase process; a knowledge booklet can help you choose sellers based on product quality, price and delivery time. During the control of purchasing processes, you may also determine whether you are dealing only with suppliers that are suitable. You can also determine whether your resellers are meeting company criteria or the requirements of purchase agreements, and can act accordingly.
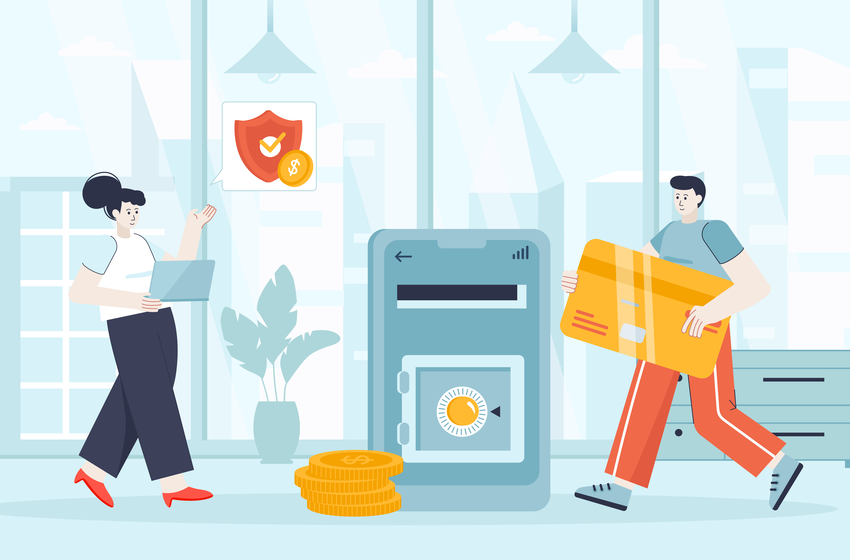
Quality Assessment
Control of the quality of the product or service is crucial in purchasing processes. The specifications or service of the Product must be reviewed in detail, whether it is truly as specified or if there is any difference.
A process you check should start with the purchase of the goods. Client returns, errors with your deliveries, and procedures used during the first delivery should be compared. The samples of damaged or defective goods should be examined and all quality matters noted meticulously. Checking all this will lead to a reduction in costs. Additionally, it will not adversely affect your relationships with your customers.
Communication
Relationships with suppliers play a key role in the purchasing process. A good supplier will ensure that the whole process goes smoothly. You should check both your company’s internal communication and your relationships with suppliers and you can see in your purchasing audit what else communication problems are causing.
Documents and workflows used in the purchasing and payment process must be presented. The available purchasing systems can provide support for potential errors and problems. The developed purchasing solutions will also facilitate coordination in integration with all other internal units. With these systems, you can take control of your supplier relationships.
More effective control of the approval process, vendor compliance, quality assessment and communication processes. This ease will protect you from critical mistakes.
You can increase efficiency and minimize the margin of error with a system that will allow you to control the control environment. However, it is necessary to perform a project management supported by the advanced strategic plans. The analyzes have to be done properly and the information should be always available. Control of purchasing processes will pave the way for growth and development.
Dominate your purchasing processes
Discover SmartProcure - the big convenience to managers and buyers - now
If You Want Call First