In order to ensure that costs and deliveries are within the proper parameters, procurement teams work on key performance indicators.
What are the purchasing criteria and performance criteria? Since the procurement department is playing an increasingly important role in the supply chain economically and especially in crises, it is important to measure the purchasing performance and to properly adopt the performance criteria.
Reducing the cost of raw materials and services, making winning moves for the business and marketing the prices of finished products competitively, would be possible if the right steps are taken. The most significant performance measure for the success of any purchasing department or your purchasing department is the amount of money saved by the company.
However, there are a number of performance criteria that businesses can use to measure purchasing performance. These include:
-
Purchase Efficiency
-
Purchasing Activity
-
Purchasing Functionality
-
Performance Metrics
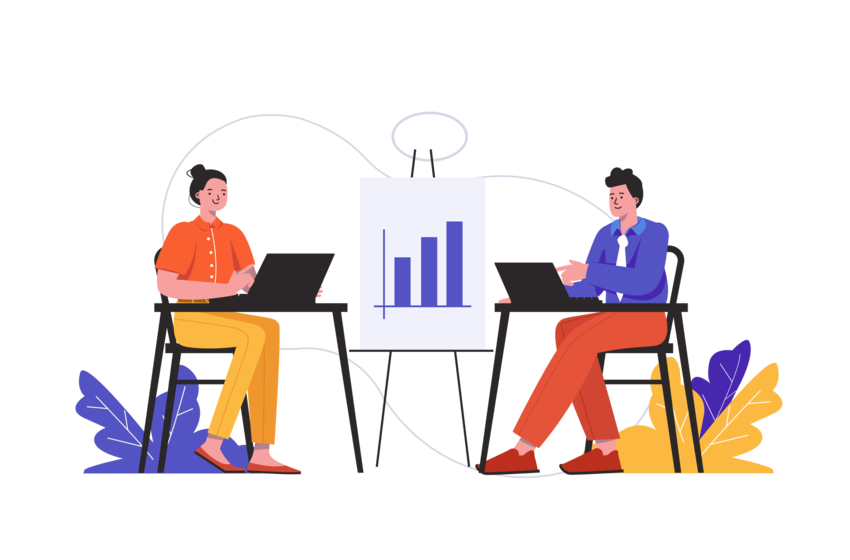
Purchase Efficiency
The price paid by the purchasing department for a product (goods or services) is not a measure of the purchasing performance, of course.
The price of a good or service (product) may fluctuate due to market conditions, availability and other demand pressure. Therefore, the purchase department may not be able to check the price. Reviewing inventory turnover rates is a popular method used to assess purchasing effectiveness. The rate measures the average number of times the inventory has been used or rotated during the period.
This rate, which is used to measure inventory liquidity, is not always a significant measure of purchasing effectiveness, as it may be inaccurate around relevant period requirements such as having stocks.
Purchasing Functionality
Purchasing performance can be measured according to the functional requirements of the purchasing function.
The main function of the department is to provide the right goods and services at the desired time at the lowest possible cost.
These elements can participate in performance metrics; however, the supplier’s commitment does not take into account factors related to material quality issues and supplier reductions. Therefore it is not completely adequate and it may be better for you to assess with other criteria.
Performance Criteria
The performance of the purchasing function can be measured using various criteria.
A company may decide which of the following activity criteria applies to the performance of its procurement department: Criteria can include:
-
Savings: If Procurement department procures a good or service at a lower price than those which it has previously purchased, then it will provide a cost saving. This can happen if a new supplier is found, a less expensive spare part is used, a new contract is signed with the seller, a cheaper method of transportation is provided or a lower price agreement has been entered into by the purchasing department with the existing supplier.
-
Increasing Quality: When a product improves quality by using or negotiating with a different supplier, improvement will be reflected in the reduction of waste or production resources.
-
Purchase Improvements: Productivity in the method used in the purchasing department will increase efficiency. This includes payment in EDI, e-procurement systems, vendor-managed inventory and receipt processes.
-
Transportation Improvements: When a procurement department negotiates with a carrier or carrier number to reduce the cost of transporting products from the vendor to the manufacturing facilities, the unit cost of the product will be reduced. This cost saving can be used as an activity measurement.
A tool that adapts to your needs
Meet SmartProcure today, answering all your purchasing needs
If You Want Call First
Purchasing Performance
A series of studies have been run on purchasing performance and results indicate that there is no method to cover each purchasing department. That is, every purchasing department and every company’s purchasing function has specific criteria and criteria. It’s up to you to make the right choices for your business against those criteria and metrics, and to shape it to your goals.
However, there are some common important criteria and measures when assessing performance. This means cost savings, supplier quality, delivery metrics, price effectiveness and inventory flow.
Although these important measures and criteria are known to be common, the weight attached to them is by no means uniform and varies between sectors and businesses. Additionally, the importance of these measures for the overall effectiveness of a procurement unit will evolve over time and should therefore be periodically evaluated and modified.